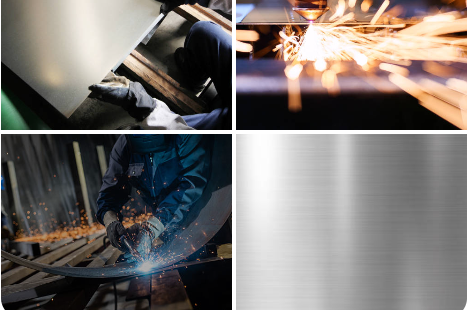
get to know us
Understanding CNC Surface Roughness and Finishing Techniques
-
In CNC machining, surface roughness is more than just a matter of appearance—it’s a critical factor that affects part performance, tolerance, and application suitability. Whether you’re producing high-precision components or functional prototypes, understanding surface roughness and the finishing techniques available can help ensure your parts meet both technical and aesthetic requirements. In this article, we’ll explore what CNC surface roughness means, how it’s measured, and the most common finishing methods used in the industry.
What Is CNC Surface Roughness?
Surface roughness refers to the fine irregularities or deviations on a machined surface. These microscopic variations are typically caused by tool marks left behind during the machining process. The level of roughness can impact factors like:
Friction and wear
Tightness of mechanical fits
Coating and bonding quality
Visual appearance
Surface roughness is typically measured in micrometers (µm) or microinches (µin), with lower values indicating smoother surfaces.
How Surface Roughness Is Measured
Surface roughness is often specified using the Ra value, which is the average roughness over a given length. Common standards include:
Ra 3.2 µm (125 µin): Standard machined finish
Ra 1.6 µm (63 µin): Fine machining finish
Ra 0.8 µm (32 µin): Smooth finish, often used for sealing surfaces
Ra 0.2 µm (8 µin) or lower: Precision-grade surface, typically achieved through grinding or polishing
Choosing the appropriate roughness depends on the part’s function and the industry requirements (e.g., aerospace, automotive, medical).
Common CNC Finishing Techniques
Several finishing techniques can be used after or during machining to improve the surface quality. Here are the most commonly used ones:
1. Grinding
Grinding uses abrasive wheels to achieve very smooth and precise surfaces, often reducing surface roughness to under Ra 0.2 µm. It’s ideal for high-precision applications.
2. Polishing
Used mainly for visual improvement and smooth finishes. Polishing is common in consumer electronics, medical parts, and decorative items.
3. Bead Blasting
Bead blasting involves blasting a surface with small glass or ceramic beads to create a uniform matte finish. It removes tool marks and gives parts a clean appearance.
4. Anodizing
While anodizing primarily serves as a protective coating for aluminum parts, it also smooths and enhances surface appearance. Type II anodizing provides color and corrosion resistance; Type III (“hardcoat”) adds extra durability.
5. Electropolishing
An electrochemical process that removes a thin layer of material from a metal surface, leaving a mirror-like finish. It’s common in stainless steel parts used in food, medical, and pharmaceutical equipment.
6. Brushing
Creates a uniform, linear texture on the surface using abrasive belts or pads. It’s often used in metal enclosures and components where aesthetics matter.
Choosing the Right Finish for Your CNC Part
When selecting a finishing technique, consider:
Functionality: Does the part require low friction, tight fits, or corrosion resistance?
Material: Not all finishes are compatible with every material (e.g., anodizing is for aluminum).
Cost: Finer finishes typically involve additional processes and higher costs.
Appearance: Consumer-facing parts may need matte, glossy, or textured finishes.
Partnering with the Right CNC Manufacturer
Working with a knowledgeable CNC machining service provider—like HTSPrecision—can help you choose the best surface finish for your application. They can provide insights into achievable roughness levels based on your design, materials, and budget.
continue reading
Related Posts
According to product design, once you decide to use CNC to process the product, you should choose the best material, whether it is metal, plastic
According to product design, once you decide to use CNC to process the product, you should choose the best material, whether it is metal, plastic
According to product design, once you decide to use CNC to process the product, you should choose the best material, whether it is metal, plastic